The Relevance of Normal Welding Inspection Milwaukee for Conformity
The Relevance of Normal Welding Inspection Milwaukee for Conformity
Blog Article
Recognizing the Relevance of Welding Evaluation in Ensuring Structural Integrity
Welding examination plays an essential duty in preserving structural stability within the building market, offering as a vital guard versus prospective failings. By methodically recognizing typical issues-- such as porosity and incomplete blend-- examinations not only support quality standards but additionally make certain conformity with security policies.
Role of Welding in Building

Along with structural applications, welding is important in the fabrication of both massive and detailed parts. It allows for the modification of parts, enabling designers and designers to bring their layouts to fulfillment. The flexibility of welding methods, including MIG, TIG, and arc welding, enables the reliable joining of different products and thicknesses, catering to certain project requirements.
In addition, the advancement of welding technologies has actually brought about enhanced effectiveness and accuracy in building processes. Automated welding systems improve efficiency while lowering human error, consequently advertising better end results. The role of welding in construction prolongs beyond simple setting up; it is an essential factor in ensuring the security, longevity, and overall stability of structures, underscoring its importance in the modern-day building landscape.
Common Welding Defects
The honesty of bonded structures is substantially affected by the presence of problems that can endanger their efficiency and safety. Common welding defects include porosity, incomplete blend, undercutting, and slag inclusions, each of which can badly affect the general toughness and toughness of bonded joints.
Porosity occurs when gas bubbles are trapped in the weld steel, leading to lowered tensile strength. Incomplete fusion occurs when the weld metal does not appropriately bond with the base steel, resulting in weak joints vulnerable to failing. Damaging, a groove that forms beside the weld, can decrease the effective cross-sectional location, boosting the risk of fracture. Slag incorporations occur when non-metallic materials end up being entraped in the weld, causing anxiety focus factors that may start splits.
Other issues, such as too much spatter and misalignment, can additionally add to architectural weak points. Recognizing and resolving these flaws during the welding procedure is vital to make sure the reliability of the final structure. Understanding of these typical welding problems is necessary for inspectors and engineers to preserve the honesty of bonded structures and make certain long-lasting safety and security and efficiency.
Advantages of Welding Inspection
Making certain the honesty of welded frameworks depends greatly on the efficiency of welding evaluation processes. The key advantage of welding assessment is the early detection of potential defects, which can considerably minimize the threat of disastrous failings. By identifying concerns such as fractures, insufficient fusion, or porosity before they intensify, inspection processes aid maintain the safety and security and reliability of structures.
In addition, welding evaluation boosts conformity with sector requirements and regulations. Sticking to these needs is essential for staying clear of lawful repercussions and making sure that projects fulfill necessary safety methods. This compliance also fosters a society of high quality guarantee, advertising ideal practices among welding workers.
Furthermore, routine assessment can lead to cost savings over time. By reducing the probability of rework or repair services as a result of welding problems, companies can designate resources more effectively, ultimately enhancing productivity.
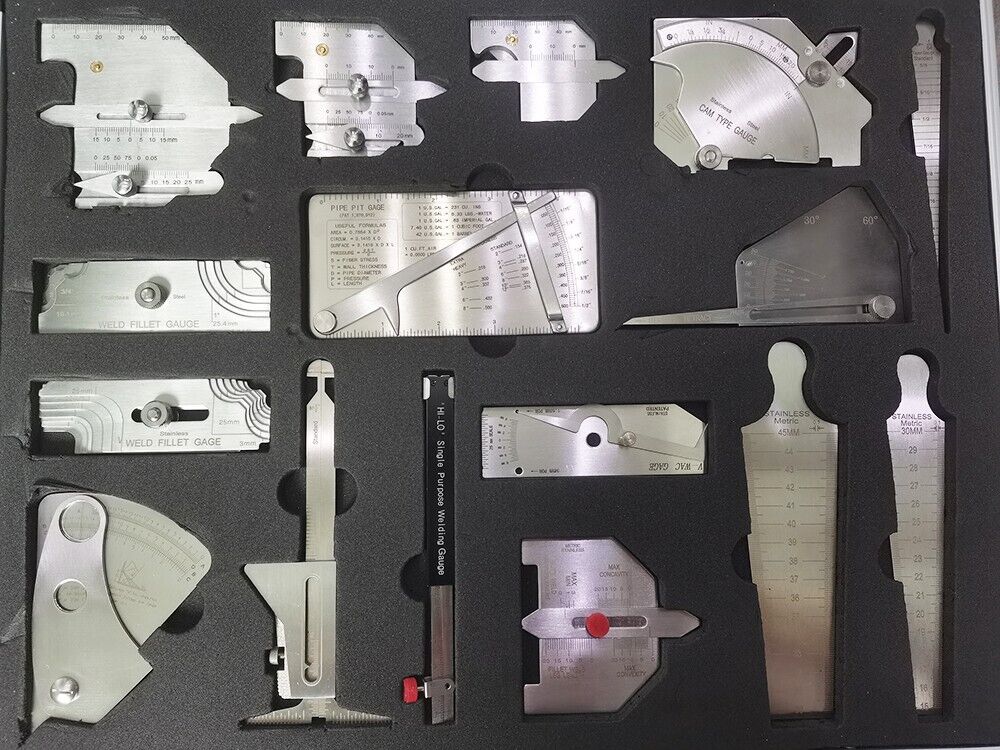
Evaluation Techniques and Specifications
Reliable assessment techniques and requirements are necessary components of preserving the integrity of welded structures. These methods make sure that welds are executed properly and satisfy the needed requirements, therefore decreasing the threat of architectural failing. Usual examination techniques include visual inspection, ultrasonic testing, radiographic testing, and magnetic bit screening. Each method has its distinct benefits and applications, depending upon the particular demands of the job.
Visual evaluation is often the very first step, enabling inspectors to determine surface issues such as splits or incorrect grain forms. Ultrasonic testing employs high-frequency acoustic waves to find internal imperfections, while radiographic screening utilizes X-rays or gamma rays to expose hidden incongruities within the weld. Magnetic bit testing is reliable for discovering surface area and near-surface defects in ferromagnetic products.
Specifications play an essential function in leading these assessment processes, with companies such as the American Welding Culture (AWS) and the International Organization for Standardization (ISO) supplying comprehensive standards. Compliance with these requirements not just makes certain the high quality of welds however additionally cultivates trust fund amongst stakeholders in the structural integrity of the finished item. Sticking to recognized evaluation techniques and criteria is essential to accomplishing reliable and durable bonded structures.
Regulatory Conformity and Security
Regulatory conformity is crucial for protecting the safety and security and stability of welded frameworks. Complying with established codes and requirements, such as those set by the American Welding Culture (AWS) and the American National Criteria Institute (ANSI), ensures that welding methods meet rigorous safety and top quality demands. These laws are created to stop failings that could cause catastrophic occurrences, injuries, or loss of life.
Compliance with these regulations includes normal evaluations and analyses throughout the welding process. Licensed assessors assess welds for top quality, strength, and adherence to requirements, ensuring that any type of inconsistencies are promptly attended to. This aggressive approach not only improves the architectural honesty of bonded components however likewise minimizes threats associated with non-compliance.
Additionally, regulative bodies usually require documentation of evaluations and compliance documents, which offer as lawful evidence of adherence to safety and security criteria. Companies that prioritize find here regulatory compliance not only protect their workforce and clients but also enhance their credibility within the market. Eventually, understanding and carrying out these guidelines is vital for any kind of organization aiming to preserve high security requirements and achieve long-term operational success in welding practices.
Verdict
In verdict, welding evaluation plays a vital function in maintaining architectural integrity within the building and construction industry. Eventually, a commitment to extensive welding inspection is necessary for protecting both the labor force and the integrity of built frameworks.
The flexibility of welding strategies, including MIG, TIG, and arc welding, enables for the reliable joining of various products and thicknesses, providing to details project demands.
Ensuring the Click Here stability of bonded frameworks relies heavily on the performance of welding inspection processes (Welding Inspection Milwaukee). In recap, the advantages of welding inspection are diverse, critical for ensuring structural stability and functional quality

Adhering to well established codes and criteria, such as those established by the American Welding Culture (AWS) and the American National Standards Institute (ANSI), guarantees that welding methods satisfy rigid safety and security and quality needs. Inevitably, a dedication to extensive welding inspection is necessary for safeguarding both the workforce and the honesty of constructed structures.
Report this page